Comtec composite technology has been used for over 45 years.
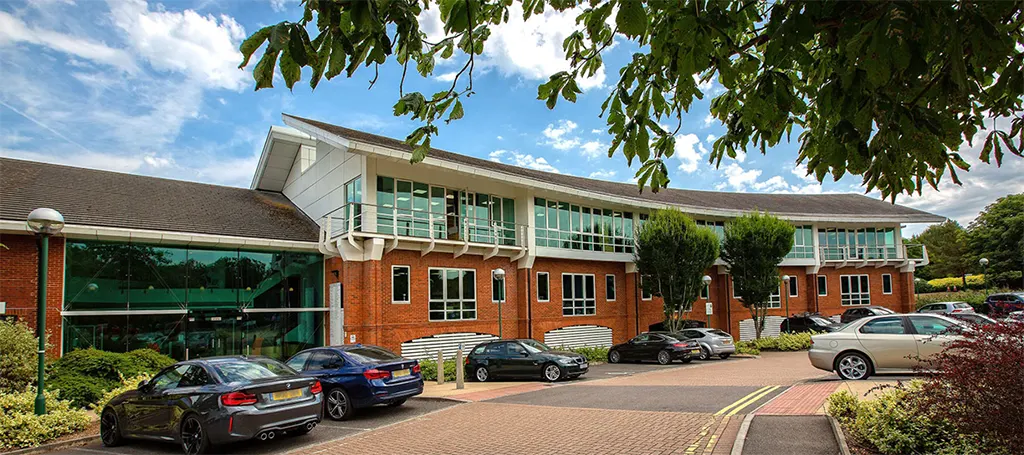
Comtec, part of MCP Group Ltd, are providers of innovative, high strength composite solutions. We specialise in creating custom, unique solutions for major projects, with an unrivalled dedication to design, engineering and customer service.
Our journey in composites began by developing composite products for use in harsh and extreme environment sectors, such as off-shore and Oil & Gas, where the values of an alternative to steel based products were of particular interest, due to to the resiliance of composite solutions we provided. Over the years Comtec manufacturing technology has been refined and now it is one of the most reliable and adaptable materials available in today’s regular construction markets, providing extensive opportunities to value engineer projects and deliver significant schedule and commercial benefits.
These GRP (glass reinforced polyester) offer unique advantages for almost any construction project, Today, Comtec composite products are used in countries around the world and in a vast range of industries; utilities, construction, infrastructure, oil & gas, data centres to name a few.
Comtec has developed strategic alliances with global leaders in the composite world to produce some of the most advanced GRP materials available today, so wherever your project is located we are able to support you in your quest to deliver improvements and added value.
Why Choose Fibreglass?
Comtec’s composites materials are made up of at least two different components, of which neither are well suited for construction purposes on their own, our unique combination results in a very sturdy and firm material.
Comtec’s composite GRP materials offer exceptional benefits to the manufacturer, installer, general public / consumer and the environment.
If you are wondering how the costs of GRP compare to an equivalent regular structural steel project then we can provide you with this. Typically, the particular commercial benefit of using GRP instead of steel is in the installation and site management costs, where the lightweight, non-weld and simple to install features offer significant savings.
The core features of Comtec Fibreglass GRP products:
Stronger than structural steel on a strength-to-weight basis. Used for building structures, walkways, platforms, etc.
Comtec’s fiberglass composite products weigh approximately 75% less than steel and 30% less than aluminum, which means lower transportation costs, easier installation and less weight in structural designs.
Comtec’s advanced manufaturing capability means that the fiberglass will not rot and is impervious to insects and a broad range of corrosive environments. Comtec GRP composites have been successfully used for indoor and outdoor applications at off-shore platforms, hotels, restaurants, chemical plants, water and wastewater treatment plants, and in many other corrosive environments.
An excellent insulator, fiberglass has low thermal and electrical conductivity, making it a popular choice in electrical applications.
Fiberglass is transparent to radio waves, microwaves, and other electromagnetic frequencies. Comtec composite products are regularly used in cellular applications due to this feature, and areas such as perimeter fencing at airports where the risk of radio interference needs to be minimised.
Fiberglass is corrosion resistant which means that the need for routine painting and repair is virtually eliminated. Therefore, Comtec’s life cycle costs are often significantly lower than traditional materials such as steel and timber.
Fiberglass is lightweight and may require less equipment, workers, and time to install. Additionally, fiberglass can be field fabricated with standard carpentry tools (using carbide or diamond blades). This means reduced risk of on-site injuries and downtimes associated with traditional materials and installation equipment.
Fiberglass products withstand weathering and intense use, providing long-lasting beauty. Once installed, Comec products are extremely low maintenance.
Sustainability
Environmental Advantages of using GRP Composites
Composite products made of Glassfibre Reinforced Polymer or GRP are viewed as an advancing material due to its superior characteristics (based on resin selection) such as high strength-to-weight ratio, commendable thermo-mechanical, and corrosion resistant properties. One can easily comprehend the usefulness of this material from these physical properties. Comtec and many markets recognise the immense potential in making durable structural systems.
- Advantages of GRP:
- GRP is light in weight and helps in cutting expenses on labour and installation. GRP increases construction speed that further reduces environmental impacts.
- Fibreglass composite materials are not just durable; they also have high strength as compared to traditional materials. Users can expect less material usage to attain better or similar performance compared to conventional materials which result in lessened resource use as well as waste production.
- GRP has great potential in further maximising the longevity of existing as well as new and structures that can resist the harsh effects of weathering, degradation, and aging in severe environments.
- GRP composite materials are extremely resistant to corrosion and rot. Besides these, they present a longer and yet more efficient service life. FRP based products hardly require an energy-intensive replacement nor much maintenance.
Recycling Advantages of GRP Products
It is possible for GRP to be recycled, however it is not currently economically viable on a large scale. This is an area that we at Comtec and the wider composite community are carrying out extensive research to find ways to utilise the product at point of disposal.
Varied recycling techniques can be implemented to develop different components, further paving the route for varied recycling avenues. These products can be formed by making use of recyclate material that is generated by crushing the composites and prepregnated wastes from off cuts when producing components to particular dimensions. The individual components which include fillers or fibres from chemical or thermal removal can be converted into components2 .
Regardless, based on research conducted, it can be deduced that the production of GRP components consumes less energy and produces less greenhouse effect verses recycling steel and aluminium. To substantiate the case, a study in Rotterdam in 20033 compared energetic values of various material options in the construction of a pedestrian bridge and yielded the results below. Clearly composites present lower energy consumption.
Table below shows comparison of energy consumed during production.
Material | % Recycled Material | Consumed Energy and Energetic Material Value (Mj/kg) |
---|---|---|
Structural Steel | 0 | 46 |
Structural Steel | 1 | 36 |
Stainless Steel | 0 | 69 |
Stainless Steel | 1 | 54 |
Composites | 0 | 33 |
Aluminium | 0 | 137 |
Aluminium | 1 | 45 |
1 Lee, L.S. & Jain, 2009, The role of FRP (GRP) composites in a sustainable world. 2 School of Metallurgy and Materials, University of Birmingham. 2010. The Reuse and Recycling of Glass Fibre Waste. Available at: http://etheses.bham.ac.uk/1342/1/Wait11MRes_A1b.pdf.
3 Daniel, Ryszard A., Environmental Considerations to Structural Material Selection for a Bridge. European Bridge Engineering Conference, Rotterdam, March 2003.
Our Services
Comtec are a full-service provider of composite materials, with manufacturing and fabrication facilities, engineering, design and installation teams in house. This allows us to collaborate with architects, contractors and end users alike to help introduce composite materials in to the design process, to deliver the multiple benefits that this brings.